“I needed process knowledge.
But the people who had it… didn’t think it was their job to share.”
The Hidden Challenge in MES Requirements Gathering
In MES implementation, we often talk about data, logic, and integration.
But one of the hardest parts has nothing to do with systems — it’s about people.
Specifically:
“How do you interview a subject matter expert who doesn’t even know they’re one?”
In my case, I was trying to map out key production flows — but there were no documented SOPs, no clear process owners, and many experienced staff didn’t realize their informal knowledge was critical.
What Made It Tricky
- Many of these operators or line leaders were hands-on experts, but they didn’t carry formal titles
- They saw MES as “someone else’s project”
- Some were even hesitant to speak up, worried they might say the “wrong” thing
As a result, early interviews felt vague:
- “I’m not sure if this is what you need.”
- “We just do it that way.”
- “I think Engineering knows better.”
What Worked Instead
Here’s what helped me unlock insights from “hidden SMEs”:
✅ 1. Observe Before You Ask
Instead of jumping straight into interviews, I spent time walking the line, watching how things were actually done.
That gave me context and helped me ask better questions — grounded in real activity.
✅ 2. Ask Specific “What If” Questions
Instead of:
“Can you explain the process?”
Try:
“What happens if the scanner doesn’t read this barcode?”
“How do you know if this part passed or failed?”
These questions triggered valuable process logic and exception flows.
✅ 3. Validate, Don’t Just Extract
I didn’t just “gather” info — I reflected it back:
“So you decide to re-scan based on visual condition — is that right?”
This helped build confidence and ensured we captured what actually happens, not what was “supposed to” happen.
Your SME Might Be…
- A senior operator who’s been doing the job for 10+ years
- A technician who adjusts machines daily but doesn’t attend meetings
- A clerk who manually updates Excel trackers based on real flow issues
They may not have the title — but they hold the logic that MES needs to reflect.
🔗 Related Posts
- Building from Ground Zero: Gathering MES Requirements
- Creating Confidence: Empowering Operators as Super Users
Final Thought
Your job is to listen between the lines, and build the system with them, not just for them.
“The most valuable MES insights don’t always come from formal meetings.
They come from people who live the process — even if they don’t know they’re the SME.“
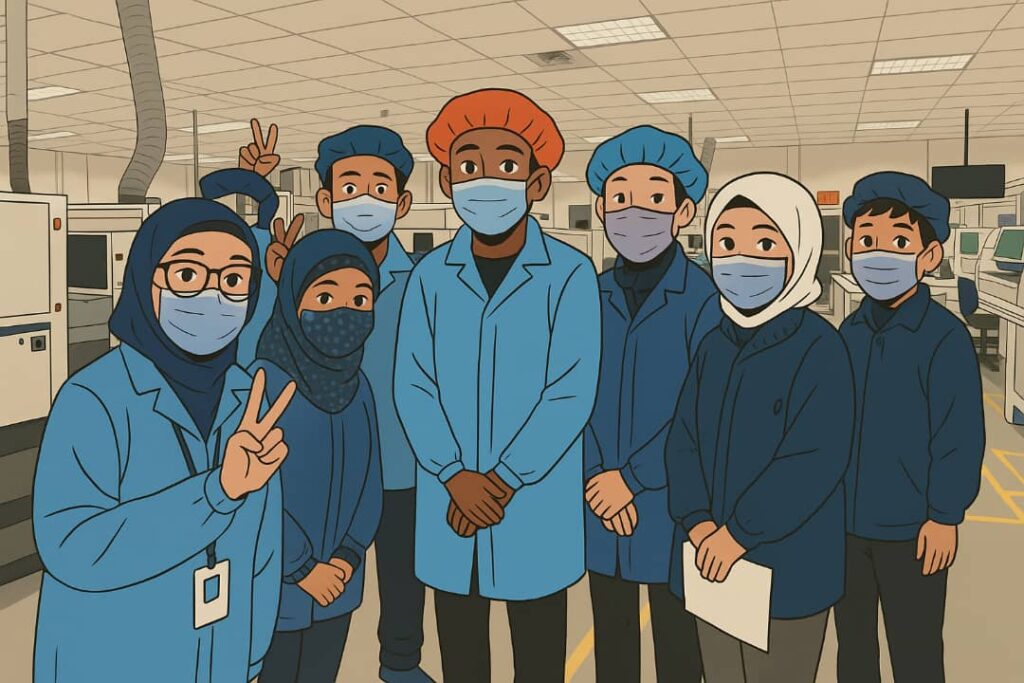